摘要:用高压釜进行热缩聚反应,对煤液化残渣精制沥青在热缩聚过程中生成的中间相沥青进行了研究。 通过元素分析、偏光显微镜对热缩聚产物进行了分析,考察了反应温度、停留时间、压力及搅拌等对中间相生成的影响。 研究表明,在410~430℃,停留4~6h条件下可以生成中间相沥青,反应初期提高压力有利于中间相的生成,有搅拌的热缩聚效果好于无搅拌的情况。
由于我国富煤、贫油的特点,煤炭一直在我国能源结构中占主导地位。 煤炭的清洁、综合利用是推动我国能源可持续发展的重要目标。 煤炭直接液化技术作为煤炭清洁利用的一项新技术,可以缓解我国的石油短缺问题。 目前我国已经建立了百万吨级煤直接液化示范装置,并且运行良好,但煤直接液化技术除了生产清洁燃料外,还会副产约占原料煤30%的煤直接液化残渣。 煤直接液化残渣是一种高灰、高硫、高碳的混合物,它的合理利用是我国煤直接液化示范装置的重要难题。 目前煤直接液化残渣的利用方式有热解[1-3]、气化[4-5]、燃烧[6-8]、加氢液化[9-10]等,但目前这些利用方式均未有工业化应用实例。 由于残渣中碳含量高,有大量的稠环芳烃化合物存在,且这些稠环芳烃作为加氢液化的产物,会有不少环烷基及侧链存在[11-13]。 因此,与煤焦油沥青相比,更容易发生热缩聚反应,是制备中间相沥青的优质前驱体[14-17]。 制备中间相沥青除了对原料要求较高外[18-21],其热缩聚的反应条件也对其生成有很大影响[22-24],本文以煤液化残渣为原料,经过溶剂萃取预处理得到低灰、低硫的煤液化残渣精制沥青[25],探索了反应条件对煤液化残渣精制沥青制备中间相沥青的影响,同时采用元素分析、偏光显微镜对中间相沥青进行研究。
1 实验
1.1 原料
试验所用的液化残渣样品来自上海煤炭直接液化中试装置(PDU)产生的液化残渣,其软化点163.5℃,沥青类物质含量48.66%。 残渣经过四氢萘溶剂萃取、离心分离后得到试验所需的煤液化残渣精制沥青,其灰分为0.02%,喹啉不溶物含量(QI)为0.8%,元素分析见表1。
1.2 热缩聚实验
为了考察煤液化残渣精制沥青热缩聚形成中间相沥青的条件,采用0.5L的高压釜进行热缩聚反应,一次放入试样量35~40g,用N2进行保护,以1~3℃/min升温速率升至反应温度,并恒温一段时间,考察反应温度、停留时间、压力及搅拌等因素对中间相沥青生成的影响。
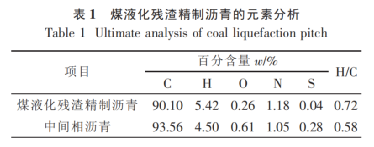
1.3 分析方法
采用德国VarioMicro型元素分析仪测定试样的元素组成; 经磨片、抛光后在ZEISSAXIOSKOP40偏光显微镜下放大500倍观察试样的偏光显微结构。
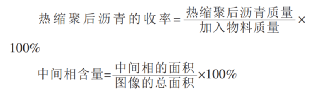
2 结果与讨论
2.1 反应温度对生成中间相沥青的影响
图1为热缩聚后沥青收率与反应温度的关系,热处理时间为4h。 可以看到,温度的升高,有利于热缩聚反应进行,温度为410℃时,热缩聚后沥青收率为78.5%,这说明煤液化残渣精制沥青中含有较多的轻组分及烷基侧链; 当温度升至420℃时,热缩聚后沥青收率降至74.3%,随着温度进一步提高至430℃,热缩聚后沥青的收率下降不明显,为72.8%,说明此时原料沥青分子中的大部分侧链已经发生断裂,剩余的大分子稠环芳烃开始发生聚合使结构进一步变大。
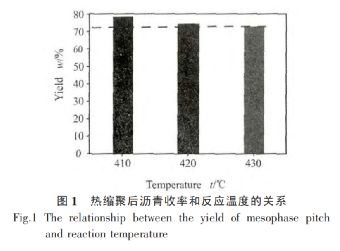
图2是不同温度下热缩聚4h产物(初始压力为常压)的偏光显微镜图。 可以看出,当温度在410℃时,已经有中间相小球出现,但小球粒径较小,且粒径尺度并不均匀,这符合均相成核的特点。 随着温度升高至420℃,中间相小球吸收母液组分及相互融并后粒径变大,当温度升至430℃时,中间相小球出现了部分融并,但由于反应时间较短,中间相未出现大面积融并的情况。
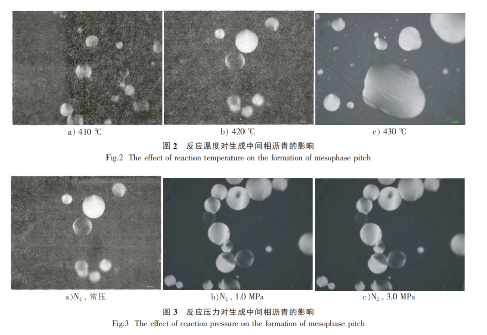
2.2 反应压力对生成中间相沥青的影响
图3考察了压力对中间相生成的影响,由图3可以看出,提高沥青热处理压力,有利于中间相沥青的生成。 这是因为提高压力可抑制沥青中小分子馏分的逸出,提高炭化率;同时使小分子馏分在较高压力下凝聚于液相之中,使黏度得到改善,流变性能更好,从而有利于小球体的融并和晶体的重排,使各向异性程度提高。 但初始压力为3.0MPa时,由于反应后期压力可达7.5MPa,压力过高,使得中间相小球的表面张力增大,反而不利于中间相的进一步融并长大。(图3b和c图片重复,应该是出版错误,所有图片来源于网络原文)
2.3 停留时间对生成中间相沥青的影响
图4为420℃、初始压力3.0MPa,不同反应时间下产物的偏光显微镜照片。 可以看出,在反应4h时已经出现了中间相小球的融并,但随着反应时间的延长,中间相小球只是变大了一些,到8h时,基本不再长大,并未出现体相中间相。 分析推测是系统压力过高造成的。 恒温420℃,反应停留时间4h时,系统压力可达7.5MPa,随着反应停留时间的增加,到8h时,系统压力已达到8.0MPa,随着时间的进一步延长压力不再升高。 反应后期压力过高,阻碍了小球进一步的融并,而且小分子馏分在较高压力下易凝聚于液相之中,降低体系黏度,随着中间相小球的融并长大,体系黏度无法维持较大的中间相小球,使其发生沉降,在底部聚集最终形成结焦物。 实验数据(表2)验证了这一推测,当反应停留时间为4h时,结焦物的生成量为12.7%,当时间为10h时,原料已大部分转化成结焦物,结焦物含量高达42.8%。
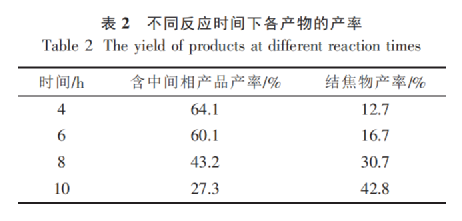
2.4 搅拌对生成中间相沥青的影响
由图5可以发现,在制备过程中进行搅拌不仅可以在中间相形成过程保持反应体系各组分的均匀性,使生成的中间相结构比较均匀,还可以在中间相形成初期抑制球体的过早融并,防止局部过热而产生结焦物,实验发现,未搅拌进行反应的产物里含有9.8%的结焦物。
2.5 中间相沥青性质分析
对煤液化残渣精制沥青在420℃炭化6h时(初始N2压力3.0MPa)得到的中间相沥青进行了性质分析。 测得其软化点为177℃,中间相沥青中含有中间相为55%,H/C原子比为0.58(见表1),而文献[13]得到的中间相沥青的软化点为270℃,H/C原子比为0.49,中间相沥青中的中间相含量几乎为100%。为了了解煤液化精制沥青制取中间相沥青的结构变化,对煤液化精制沥青及中间相沥青也进行了红外分析,结果见图6。 从图6 可以看到,3041.0,1598.5,1439.0cm-1处吸收峰相对增强,2916.1cm-1附近吸收峰相对减弱,这说明在煤液化精制沥青热转化制取中间相沥青的过程中会发生环化、脱氢、聚合、芳构化等化学反应。810.7cm-1和747.1cm-1吸收峰的存在说明在热转化过程中芳环上烷基侧链会发生断裂,这些烷基侧链断裂后使体系中存在大量的自由基,断裂的侧链为较小分子,在高压下以液相存在,可以作为大分子芳烃的溶剂提高体系的流动性,有利于大芳烃平面在热扩散及分子间力的作用下平行堆积;另外,这些小分子作为供氢剂,可以使自由基稳定化,抑制大分子的过度缩聚,这与其软化点相对较低,H/C原子比相对较高的结论相一致。
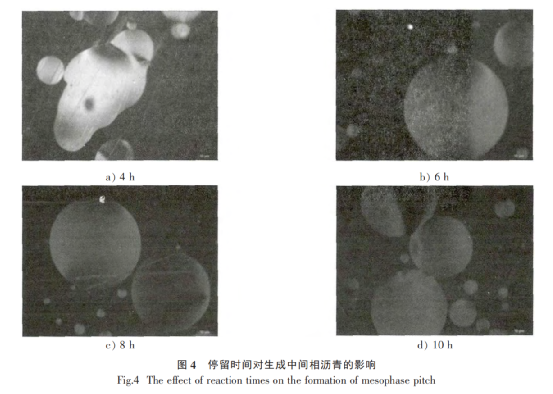
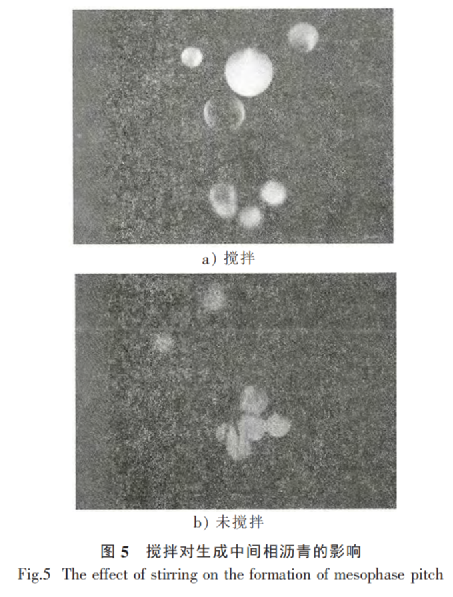
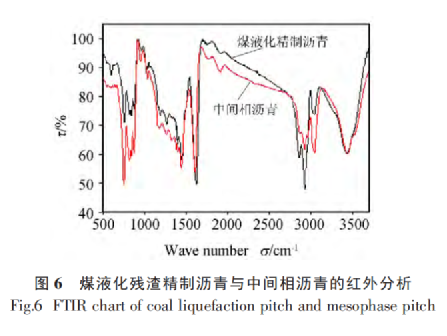
3 结语
以煤液化残渣精制沥青为原料进行了制取中间相沥青的研究,考察了不同转化条件对中间相沥青的影响,发现温度的升高、压力的提高及有一定的搅拌,均有利于中间相沥青的生成,延长停留时间,也有利于中间相沥青的生成,但同时也会提高结焦物的产率。 温度420℃,初始压力3.0MPa,时间6h为制备中间相沥青的较优条件,此时得到的中间相沥青中中间相含量为55%,软化点为177℃。