摘要:为制备优质的中间相沥青,以煤液化沥青为原料,在不同热聚合温度下制备中间相沥青,采用偏光显微镜、红外光谱仪、XRD、热分析等测试仪器对所得中间相沥青进行分析和表征。结果表明,温度对中间相沥青的收率、形貌和结构影响显著。随着温度升高,中间相沥青的收率降至86.2%,H含量降至3.96%,S含量有所下降,残炭率增大;中间相小球体的尺寸增大,逐渐出现融并现象,最终形成广域型中间相;煤液化沥青中的稠环芳烃、芳香烃的含量明显增加,烷烃成分则明显减少;煤液化沥青中的无定型区含量减少,分子的排列与取向性变好。选择低的热缩聚温度(410~420℃),适当延长反应时间有利于反应方向的控制,从而达到制备优质中间相的目的。
引言
煤直接液化油渣由煤经高温高压加氢后未转化的煤、沥青质、重质油和无机物组成,其中沥青质与重质油约占50%。将煤直接液化油渣用溶剂萃取经过脱灰后得到的物质为煤液化沥青。该沥青除具有煤焦油沥青和石油沥青的一些特性之外,还具有其自身的特点,如氢碳比高,沥青高温融变性好,硫含量低,是炭素行业理想的原料。煤沥青制备中间相沥青受到相关研究者的重视。花双平等[1-2]以煤焦油沥青为原料制备中间相沥青,发现过高聚合温度使反应过于剧烈,体系内沥青分子过度脱氢和聚合;而当聚合温度不太高,适当延长时间更有利于中间相形成及融并。崔豫泓等[3]采用3种煤沥青为原料制备中间相沥青也得到了类似结论。吕婧等[4]以中温煤沥青为原料制备中间相沥青,发现温度对中间相沥青的形成影响较大,压力对中间相的含量和结构也有一定影响。前人主要采用煤沥青制备中间相沥青[5-7],对煤液化沥青制备中间相沥青研究较少。笔者以煤液化沥青为原料,在不同热聚合温度下制备得到中间相沥青,采用偏光显微镜、红外光谱仪、XRD、热分析等测试仪器对所得中间相沥青进行分析和表征,以期制备出优质的中间相沥青。
1、试验
1.1 试验原料
试验选用中国神华煤制油化工有限公司上海研究院在500kg/d的残渣萃取装置上得到的煤液化油渣萃取物为原料(即煤液化沥青),其基本性质见表1。

1.2 热聚合反应
采用美国PARR公司的4583型3.75L高压反应釜进行煤液化沥青的热聚合反应。升温速率为2~3℃/min,氮气气氛,以恒定的搅拌速度,0.2MPa压力,恒温7h后,冷却降温到室温,即得中间相沥青。
1.3 样品分析
中间相沥青的光学显微结构观测采用德国蔡司公司生产的Axioskop40APol型偏光显微镜。热重试验采用美国TA仪器公司生产的SDT-Q600同步热分析仪测试,样品用量约10mg,N2作保护气,气体流量100mL/min,升温速率10℃/min,由室温加热到终温1000℃。红外分析采用美国ThermoNicolet公司生产的NEXUS型傅里叶变换红外光谱仪测试,扫描次数为128次,分辨率为4cm-1。XRD表征在荷兰PANALYTICAL公司的X'PertPRO衍射仪上进行,分析条件为:Cu/Kα线(0.154nm),管压40kV,管流40mA,扫描速度2(°)/min,步长0.017°。
2 结果与讨论
2.1 热聚合温度对中间相沥青性质的影响
在热聚合温度410~440℃、热聚合时间7h、热聚合压力0.2MPa的条件下,研究温度对煤液化沥青热聚合收率的影响,结果如图1所示。由图1可知,煤液化沥青热聚合的收率随温度升高而快速下降,这是因为煤液化沥青在热聚合时发生了剧烈的热缩聚反应,形成自由基,随着温度的升高,形成的自由基增加,从而释放的轻组分气体增多。
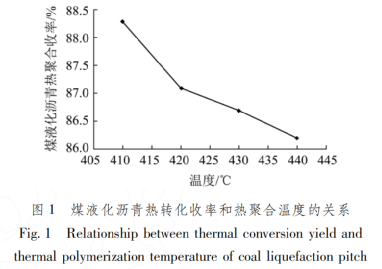
煤液化沥青和不同温度下热聚合产物的元素分析及软化点见表2。由表2可知,与煤液化沥青相比,经过热聚合后的中间相沥青(以440℃为例)的C含量从90.54%增加到95.72%,H含量从5.23%下降到3.96%,S含量从0.08%下降到0.07%,N含量变化不大。说明中间相沥青形成过程中伴随着剧烈的热缩聚反应,形成自由基,且以脱氢缩聚为主,正是通过自由基之间的聚合向芳构化和稠环化方向发展,形成中间相沥青基分子。随着聚合温度的升高,大量的小分子物质挥发,中间相沥青的软化点呈现不断增加的趋势[8-10]。聚合温度为410℃,中间相沥青的软化点为205℃,当聚合温度上升到420℃时,中间相沥青的软化点迅速增加,为343℃,说明410~420℃是中间相微晶生长以及中间相小球大量增长的阶段。当聚合温度上升到430和440℃后,最终形成了半焦,无法软化。虽然提高反应温度可以缩短中间相的转化时间,但是却使得软化点迅速提高,不利于制备优质的中间相沥青。
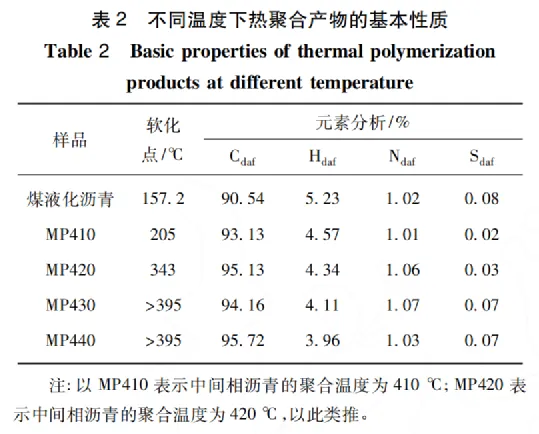
不同热聚合温度下得到的中间相沥青的偏光显微照片如图2所示。由图2(a)可知,410℃条件下制备的中间相沥青只出现了中间相小球。伴随着原料沥青中的小分子轻组分挥发,原料沥青开始发生缩聚反应生成具有中间相性质的大分子,大分子成长并聚集到一定浓度后形成中间相小球体。随着温度的升高,中间相小球吸收母液组分开始长大达到一定尺寸后,出现融并现象(图2(b))。聚合温度达到430℃时,形成了广域结构(图2(c)),在440℃时出现了中间相的取向固化(图2(d))。
2.3 TG/DTG分析
煤液化沥青与中间相沥青(以420℃为例)的TG和DTG曲线如图3所示。由图3可知,煤液化沥青与中间相沥青开始失重温度均大于200℃。升温至200℃后,煤液化沥青的热失重曲线TG下降很快,DTG曲线出现一个明显的峰,残炭率迅速降低,此阶段主要发生沥青的热分解和热缩聚并析出轻油和烃类气体等。而中间相沥青的热失重曲线下降比较平缓,DTG曲线也出现了一个明显的峰,但热失重速率明显要低于煤液化沥青。550℃后煤液化沥青与中间相沥青继续失重,但失重率较小,失重曲线比较平缓。1000℃时,煤液化沥青残炭率为33.70%,而中间相沥青的残炭率达到70.54%。这主要是中间相沥青经过热聚合后,稠环芳烃、芳香烃含量明显增加,成为中间相沥青的主要部分,烷烃成分则明显减少[11-12]。
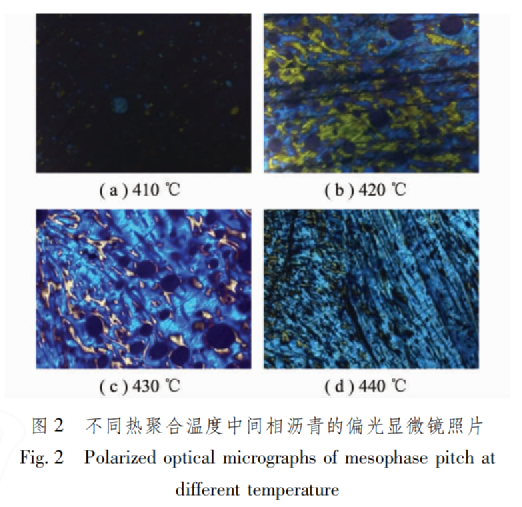
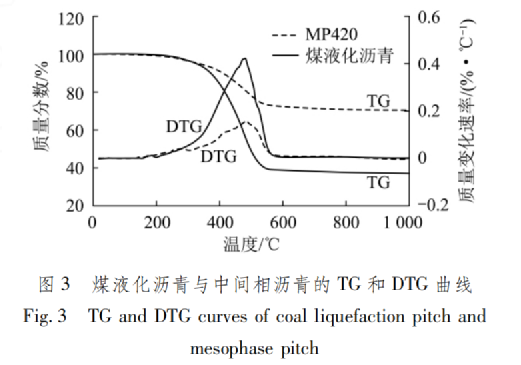
煤液化沥青与不同热聚合温度得到的中间相沥青的TG曲线如图4所示。
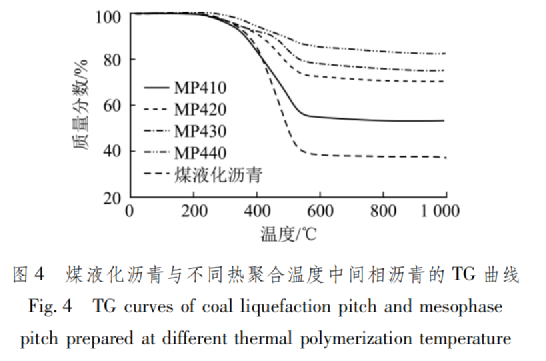
由图4可知,随着热聚合温度的升高,中间相沥青的失重曲线下降后逐渐平缓。1000℃时,煤液化沥青的残炭率为33.70%;热聚合温度为410℃时,残炭率为53.36%;聚合温度提高到420和430℃时,残炭率分别上升为70.54%和75.20%;聚合温度为440℃时,残炭率达到82.82%。这是由于随着聚合温度的升高,煤液化沥青中挥发掉的小分子物质越多,这从表2沥青的软化点变化也能看出,随着聚合温度升高,中间相沥青的软化点升高。
3.4 FTIR和XRD分析
采用红外光谱法和X射线衍射法对煤液化沥青和中间相沥青进行分析,研究中间相沥青形成机理。煤液化沥青与不同热聚合温度制备的中间相沥青的红外光谱图如图5所示。由图5可知,煤液化沥青经过热处理之后红外光谱的烷基吸收峰、芳烃吸收峰发生了较大的变化。随着热聚合温度的升高,在2859、2925cm-1处2个较强脂肪族的甲基、亚甲基以及次甲基的C—H面内对称和不对称振动峰的强度减小,而3043cm-1处芳环的C—H伸缩振动吸收峰强度明显增加。这表明煤液化沥青经过热处理后,稠环芳烃、芳香烃含量明显增加,成为中间相沥青的主要部分,烷烃成分则明显减少[4]。
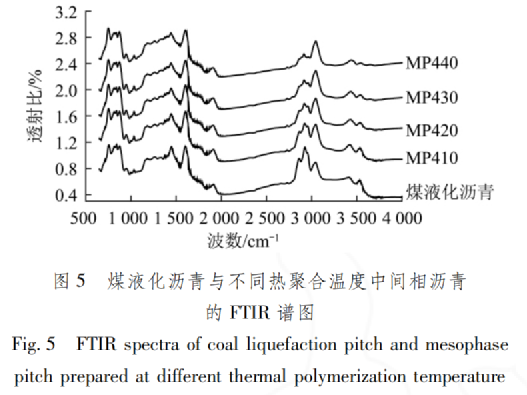
煤液化沥青与不同热聚合温度制备的中间相沥青的XRD图谱如图6所示。由图6可知,煤液化沥青经过热处理后内部结构发生了较大变化。随着温度的升高,热聚合后的中间相沥青在2θ002处的衍射强度增强,衍射峰变窄。
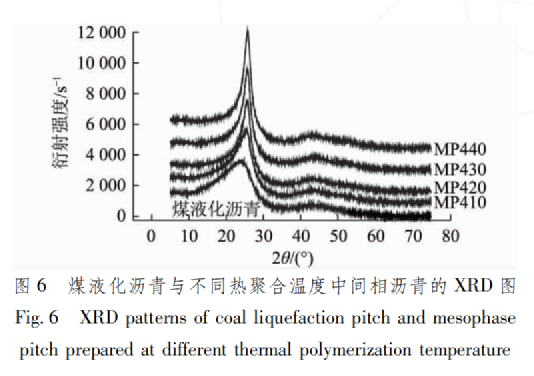
根据XRD图谱计算得到微晶参数,结果见表3。由表3可知,随着温度的升高中间相沥青在(002)晶面上的衍射强度有所加强,衍射峰变窄,其内部晶面间距d002减小,碳原子层面堆积高度Lc增大。说明通过热处理,煤液化沥青中的无定型区含量明显减少,随着中间相含量的增加,形成了较规整的片层结构[4]。
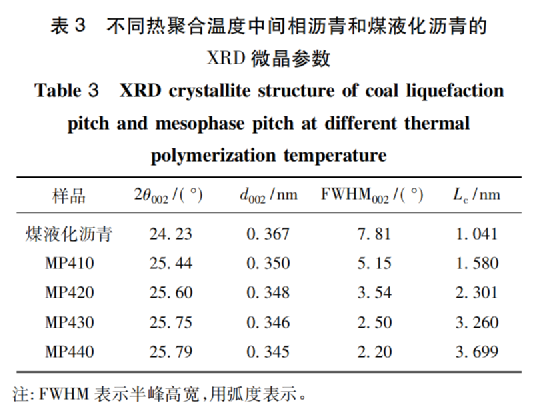
结论
1)以煤液化沥青为原料,采用热聚合法制得中间相沥青。随着热聚合温度的升高,大大缩短了中间相转化的时间,但形成的中间相沥青软化点很高,很难再软化,选择低的热缩聚温度,适当延长反应时间有利于反应方向的控制,从而达到制备优质中间相的目的。随着聚合温度的升高,中间相沥青的收率、H含量和S含量下降,N含量变化不大。
2)由FTIR分析可知,煤液化沥青比中间相沥青具有更多的烷基侧链,随着聚合温度的升高,煤液化沥青中的稠环芳烃、芳香烃的含量明显增加,成为中间相沥青的主要部分,烷烃成分则明显减少。
3)XRD分析显示随着聚合温度的升高,煤液化沥青中的无定型区含量减少,中间相含量增加,形成了较规整的片层结构。热分析显示由于稠环芳烃、芳香烃的含量明显增加,中间相沥青的残炭率比煤液化沥青大。